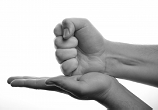
Engineering
Here are 10 facts about multi-story buildings, useful for students:
- Definition: Multi-story buildings have more than one story, allowing for greater use of land area.
- History: Ancient examples include Roman apartment buildings ("insulae") and medieval tower houses. Britannica
- Materials: Common construction materials are steel, concrete, and reinforced concrete for strength.
- Purpose: They serve various purposes, including residential (apartments), commercial (offices), and mixed-use.
- Elevators: Elevators are essential for vertical transportation in buildings exceeding a few stories.
- Structural Design: Structural engineers carefully design them to withstand gravity, wind, and seismic forces.
- Fire Safety: Fire safety measures like sprinklers, fire-resistant materials, and emergency exits are crucial. NFPA
- Sustainability: Modern multi-story buildings often incorporate sustainable design elements like green roofs and energy-efficient systems. WBDG
- Urban Density: They contribute to higher population densities in urban areas, reducing urban sprawl.
- Tallest Buildings: The tallest buildings are skyscrapers, defined by their exceptional height and complex engineering. CTBUH
The insulation of a cable depends on several factors, including:
-
Voltage Level:
The higher the voltage that the cable needs to withstand, the thicker and more robust the insulation must be. High-voltage cables require more substantial insulation to prevent electrical breakdown and ensure safe operation.
-
Operating Temperature:
The ambient temperature and the heat generated by the cable's current affect the insulation material's performance. Cables operating in high-temperature environments require insulation materials that can withstand the heat without degrading.
-
Environmental Conditions:
Exposure to moisture, chemicals, UV radiation, and other environmental factors can degrade insulation over time. Cables used in harsh environments require insulation materials specifically designed to resist these conditions.
-
Cable Material:
The material of the conductor (e.g., copper, aluminum) and the surrounding materials influence the choice of insulation. Compatibility between the conductor and insulation material is crucial for long-term reliability.
-
Insulation Material Properties:
Different insulation materials have varying dielectric strength, temperature resistance, and flexibility. The selection of the insulation material depends on the specific application requirements. Common insulation materials include PVC, XLPE, rubber, and silicone.
-
Cable Standards and Regulations:
Cables must comply with relevant industry standards and regulations, such as those set by organizations like the IEC (International Electrotechnical Commission) and national standards bodies. These standards specify minimum insulation requirements for different cable types and applications. IEC
Cantilever Beam Design - Circular Cross-Section
Problem Statement:
Design a cantilever beam with a circular cross-section to support a load, limiting the maximum bending stress.
- Span (L): 3.2 meters
- Maximum Allowable Bending Stress (σmax): 15 N/mm²
Assumptions:
- The load is applied at the free end of the cantilever beam.
- The material is homogeneous and isotropic.
- The beam is perfectly straight.
- Shear stress is not a primary design factor in this case. We are focusing on bending stress.
Design Steps:
-
Determine the Maximum Bending Moment (M):
First, we need to assume a load (W) at the free end of the beam. Let's assume a load for now and iterate if the resulting diameter is impractical. Assume W = 100 N.
For a cantilever beam with a point load at the free end, the maximum bending moment occurs at the fixed end and is calculated as:
M = W * L
M = 100 N * 3200 mm = 320,000 N·mm
-
Calculate the Required Section Modulus (Z):
The bending stress (σ) is related to the bending moment (M) and section modulus (Z) by the following formula:
σ = M / Z
Therefore, the required section modulus is:
Z = M / σmax
Z = 320,000 N·mm / 15 N/mm² = 21,333.33 mm³
-
Determine the Diameter (d) of the Circular Cross-Section:
For a circular cross-section, the section modulus (Z) is given by:
Z = (π * d³) / 32
Where 'd' is the diameter of the circle.
Solving for 'd':
d³ = (32 * Z) / π
d³ = (32 * 21,333.33 mm³) / π ≈ 217,146.98 mm³
d = ∛217,146.98 mm³ ≈ 60.07 mm
-
Select a Suitable Diameter:
Choose a standard or readily available diameter slightly larger than the calculated value. For example, select d = 65 mm. This provides a small safety margin.
-
Verify the Bending Stress:
Recalculate the section modulus (Z) with the chosen diameter:
Z = (π * (65 mm)³) / 32 ≈ 27,150.75 mm³
Calculate the actual bending stress:
σ = M / Z = 320,000 N·mm / 27,150.75 mm³ ≈ 11.79 N/mm²
Since 11.79 N/mm² < 15 N/mm², the design is acceptable for the assumed load of 100N.
Iteration (Important!):
The above calculation was based on an assumed load of 100 N. This is unlikely to be the *actual* load. The *actual* load the beam will experience needs to be determined through a different method.
To complete the design:
- Determine the actual load (W) that the cantilever beam needs to support based on the application.
- Repeat steps 1-5 using the *actual* load (W).
Without knowing the real load, it is impossible to complete the beam design. This process shows how to select the correct diameter when that load is known.
Important Considerations:
- Material Selection: The material's yield strength must be significantly higher than the calculated bending stress, including a factor of safety. Common materials include steel, aluminum, or composites. The elastic modulus (Young's Modulus) is also important for deflection calculations (not performed here).
- Deflection: Calculate the maximum deflection of the cantilever beam to ensure it meets the application's requirements. The deflection should be within acceptable limits.
- Shear Stress: While bending stress is the primary concern here, check shear stress, especially near the fixed end. For circular cross-sections, shear stress is often less critical than bending stress, but should still be checked.
- Buckling: If the beam is very long relative to its diameter, consider buckling. This is less likely to be an issue for typical cantilever beam proportions but should be checked for slender beams.
- Manufacturing Tolerances: Account for manufacturing tolerances in the diameter.
Cantilever Beam Design for Bending Press
1. Problem Definition:
- Span (L): 3.2 meters (3200 mm)
- Maximum Allowable Bending Stress (σmax): 50 N/mm²
- Beam Type: Cantilever with circular cross-section
2. Material Selection:
We will initially consider structural steel (e.g., ASTM A36) due to its common usage and availability. However, the final material selection depends on factors like cost, weldability, and desired lifespan. For initial calculations, assume:
- Yield Strength (σy): 250 N/mm² (for A36 steel - this is just for reference and not used in the bending stress calculation directly but informs the factor of safety) Engineering ToolBox - ASTM A36 Steel
3. Load Estimation:
This is the most critical and least defined part of the problem. We must estimate the maximum force (F) that the bending press will apply at the end of the cantilever beam. Without this, we cannot complete the design.
Assume for this example: The bending press will exert a maximum force of 10,000 N (1 metric ton) at the end of the beam.
4. Bending Moment Calculation:
For a cantilever beam with a point load (F) at the free end, the maximum bending moment (M) occurs at the fixed end and is given by:
M = F * L
M = 10,000 N * 3200 mm = 32,000,000 N·mm
5. Section Modulus Calculation:
The bending stress (σ) is related to the bending moment (M) and section modulus (Z) by:
σ = M / Z
Therefore, Z = M / σ
Z = 32,000,000 N·mm / 50 N/mm² = 640,000 mm³
6. Diameter Calculation:
For a circular cross-section, the section modulus (Z) is given by:
Z = (π * d³) / 32
Where 'd' is the diameter of the circular cross-section.
Therefore, d³ = (32 * Z) / π
d³ = (32 * 640,000 mm³) / π ≈ 6,517,946 mm³
d = ∛6,517,946 mm³ ≈ 187.1 mm
Therefore, we will choose a diameter of 190 mm as a starting point for our design.
7. Deflection Check:
It's essential to verify that the deflection is within acceptable limits. The maximum deflection (δ) for a cantilever beam with a point load at the free end is:
δ = (F * L³) / (3 * E * I)
Where:
- E is the modulus of elasticity of the material (e.g., for steel, E ≈ 200,000 N/mm²)
- I is the second moment of area (moment of inertia) of the circular cross-section. For a circle, I = (π * d⁴) / 64
Calculate I: I = (π * (190 mm)⁴) / 64 ≈ 63.9 x 106 mm4
Calculate Deflection: δ = (10,000 N * (3200 mm)³) / (3 * 200,000 N/mm² * 63.9 x 106 mm4) ≈ 8.52 mm
This deflection should be assessed for suitability in the application. If the deflection is too high, consider increasing the diameter further.
8. Factor of Safety:
The design should incorporate an appropriate factor of safety. A common factor of safety for structural steel applications is between 1.5 and 3. Since we are limiting bending stress to 50 N/mm2, which is much smaller than the yield strength, the factor of safety is intrinsically high. However, buckling needs to be considered.
9. Buckling Check:
Cantilever beams under bending can be susceptible to lateral-torsional buckling, especially with long spans. This is particularly true for beams with cross-sections that are not very rigid in the lateral direction. A circular cross-section is excellent in this regard, but it should still be checked, particularly if the force estimate turns out to be significantly higher.
A detailed buckling analysis requires more information about the specific application and support conditions. Simplified buckling checks can be performed using Euler's formula with appropriate effective length factors. This is a critical step that requires specialist engineering knowledge, and must be investigated during detailed design.
10. Assembly and Support:
The fixed end of the cantilever beam must be rigidly supported. This usually involves welding or bolting the beam to a robust frame or structure. The support structure must be capable of withstanding the reaction forces and moments from the beam. The design of the support is as important as the beam itself.
- Welding: If welding is used, ensure the weld is strong enough to withstand the bending moment and shear force at the fixed end. Use appropriate welding procedures and qualified welders.
- Bolting: If bolting is used, calculate the required number and size of bolts based on the reaction forces and moments. Use high-strength bolts and ensure proper pre-tensioning.
11. Further Considerations:
- Manufacturing Tolerances: Account for manufacturing tolerances in the diameter and length of the beam.
- Surface Finish: Consider the required surface finish for the application.
- Corrosion Protection: Implement appropriate corrosion protection measures, such as painting or galvanizing, if the beam will be exposed to corrosive environments.
- Dynamic Loading: If the bending press will be subjected to dynamic loads, perform a fatigue analysis to ensure the beam can withstand repeated loading cycles.
- Finite Element Analysis (FEA): For a more detailed analysis, especially concerning buckling and stress concentrations at the support, consider using FEA software.
Summary
- Based on the assumptions above (a 10,000 N load), a 190 mm diameter circular steel beam is a reasonable starting point.
- Buckling must be investigated by a qualified engineer.
- The deflection check is important and must be assessed in the application.
- The fixed end support design is critical and must be robust.
Here are the key differences between 2-stroke and 4-stroke engines:
1. Cycle of Operation:
- 2-Stroke Engine: Completes a power cycle with one up and one down movement of the piston (one revolution of the crankshaft).
- 4-Stroke Engine: Completes a power cycle with two up and two down movements of the piston (two revolutions of the crankshaft).
2. Mechanical Simplicity:
- 2-Stroke Engine: Generally simpler in design, with fewer moving parts (no valves or complex valve train).
- 4-Stroke Engine: More complex, with valves, camshafts, and a more intricate valve train system.
3. Power Output:
- 2-Stroke Engine: Theoretically, for a given size, a 2-stroke engine can produce twice the power of a 4-stroke engine because it fires once every revolution instead of every other revolution. However, in practice, the difference is less pronounced due to other factors.
- 4-Stroke Engine: Generally produces more usable torque and power over a broader RPM range.
4. Fuel Efficiency:
- 2-Stroke Engine: Typically less fuel-efficient because some of the fuel-air mixture is lost during the scavenging process.
- 4-Stroke Engine: More fuel-efficient due to better control of the intake and exhaust processes.
5. Lubrication:
- 2-Stroke Engine: Lubrication is typically mixed with the fuel or injected directly into the engine. This results in the oil being burned along with the fuel.
- 4-Stroke Engine: Has a separate lubrication system with an oil sump and pump to circulate oil throughout the engine.
6. Emissions:
- 2-Stroke Engine: Generally produces higher emissions because of the loss of fuel during scavenging and the burning of oil.
- 4-Stroke Engine: Produces lower emissions due to more complete combustion and separate lubrication.
7. Maintenance:
- 2-Stroke Engine: Can be easier to maintain due to its simpler design, but may require more frequent servicing.
- 4-Stroke Engine: Generally requires less frequent servicing, but maintenance can be more complex due to the intricate valve train.
Preparing heavily rusted mild steel for welding is crucial to ensure a strong, sound weld. Rust can contaminate the weld pool, leading to porosity, lack of fusion, and reduced weld strength. Here's a step-by-step approach:
1. Initial Cleaning and Inspection:
-
Visual Inspection: Assess the extent of the rust and check for any other defects like cracks or significant material loss due to corrosion.
-
Initial Cleaning: Remove loose rust, scale, dirt, and debris with a wire brush, scraper, or chipping hammer. This initial cleaning helps to evaluate the severity of the rust and plan subsequent steps.
2. Mechanical Cleaning Methods:
-
Grinding: Use a grinder with a coarse grinding wheel, flap disc, or abrasive disc to remove the bulk of the rust. Be careful not to gouge the base metal. Gradually move to finer grits for a smoother surface. MillerWeld - Preparing Metal for Welding
-
Sanding: Similar to grinding, sanding can be used with different grit levels to remove rust and smooth the surface.
-
Abrasive Blasting: Sandblasting, bead blasting, or media blasting is highly effective for removing rust, especially in hard-to-reach areas. This method uses abrasive materials propelled at high speed to remove surface contaminants. TWI-Global - Surface preparation of steels for welding
-
Wire Brushing (Power Tools): Using a power drill or angle grinder with a wire brush attachment can effectively remove rust, scale, and other surface contaminants. Ensure you wear appropriate safety gear, including eye protection and a respirator.
3. Chemical Cleaning (If Necessary):
-
Rust Converters: Apply a rust converter containing phosphoric acid or tannic acid. These chemicals react with the rust, converting it into a more stable compound that can be painted over. Follow the manufacturer's instructions carefully. Note: Welding over rust converter residue is generally not recommended, so ensure that the treated area is thoroughly cleaned before welding. If any doubt exists, remove it completely by mechanical means.
-
Acid Pickling: In industrial settings, acid pickling (using solutions like hydrochloric or sulfuric acid) can be used to remove rust. This method requires careful handling and proper disposal of the acid. Note: Thoroughly neutralize and clean the metal after pickling to remove any acid residue. This method is often impractical for small-scale welding projects.
4. Final Preparation Before Welding:
-
Degreasing: Remove any oil, grease, or other contaminants with a suitable degreaser or solvent cleaner. Use a clean cloth or paper towel to wipe the surface dry. Contaminants can cause porosity and weaken the weld.
-
Edge Preparation: Bevel the edges of thicker materials to ensure adequate weld penetration. This creates a V-groove or U-groove that allows the weld to fully penetrate the joint.
-
Fit-Up: Ensure proper fit-up and alignment of the parts to be welded. Use clamps, jigs, or tacks to hold the pieces in place.
-
Dry Run: Perform a dry run (without welding) to check the fit-up and accessibility of the joint. Adjust as necessary.
5. Welding Considerations:
-
Welding Process: Choose a welding process appropriate for the material and thickness. Shielded Metal Arc Welding (SMAW/Stick), Gas Metal Arc Welding (GMAW/MIG), and Gas Tungsten Arc Welding (GTAW/TIG) are commonly used for mild steel. Lincoln Electric - Choosing a Welding Process
-
Welding Parameters: Select appropriate welding parameters (voltage, amperage, travel speed) for the welding process, material thickness, and joint configuration. Consult welding charts or guidelines for recommended settings. Test welds can help dial in the settings. ESAB - Welding parameters
-
Welding Technique: Use proper welding techniques to ensure good penetration, fusion, and weld quality. Maintain a consistent arc length, travel speed, and electrode angle.
-
Multi-Pass Welding: For thicker materials or critical applications, use multi-pass welding to build up the weld in layers. Clean each pass with a wire brush to remove slag or other contaminants before applying the next pass.
Safety Precautions:
-
Always wear appropriate personal protective equipment (PPE), including a welding helmet, gloves, safety glasses, hearing protection, and a respirator (especially when grinding, blasting, or welding in enclosed spaces).
-
Ensure adequate ventilation to remove fumes and dust.
-
Follow all safety guidelines and procedures for welding and using power tools.
By following these steps, you can effectively prepare heavily rusted mild steel for welding, resulting in a strong, reliable weld.