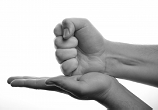
Quality Control
0
Answer link
To control the quality of incoming goods, I would implement a comprehensive system with several key components:
1. Supplier Qualification and Management:
- Supplier Selection: Establish strict criteria for selecting suppliers, including quality certifications (e.g., ISO 9001), past performance, financial stability, and adherence to ethical standards.
- Supplier Audits: Conduct regular audits of supplier facilities to assess their quality control processes, manufacturing capabilities, and compliance with requirements.
- Supplier Agreements: Develop formal agreements with suppliers that clearly define quality expectations, acceptance criteria, and procedures for handling non-conforming goods.
- Performance Monitoring: Continuously monitor supplier performance based on key metrics such as defect rates, on-time delivery, and responsiveness to issues.
2. Receiving Inspection:
- Inspection Plans: Develop detailed inspection plans for each type of incoming material, specifying the characteristics to be inspected, the sampling methods to be used, and the acceptance criteria.
- Trained Inspectors: Ensure that receiving inspectors are properly trained and equipped to perform their duties effectively.
- Inspection Equipment: Provide inspectors with the necessary tools and equipment to accurately measure and test incoming materials.
- Documentation: Maintain accurate records of all inspections, including the results of tests and measurements, any non-conformances found, and the corrective actions taken.
3. Sampling and Testing:
- Statistical Sampling: Use statistical sampling techniques to select representative samples of incoming materials for inspection and testing.
- Testing Procedures: Establish standardized testing procedures for each type of material, using appropriate testing methods and equipment.
- Laboratory Analysis: Utilize in-house or external laboratories to conduct more complex testing, such as chemical analysis or material testing.
4. Non-Conforming Material Control:
- Identification and Segregation: Immediately identify and segregate any non-conforming materials to prevent their use in production.
- Investigation: Investigate the root cause of the non-conformance and implement corrective actions to prevent recurrence.
- Disposition: Determine the appropriate disposition of non-conforming materials, such as returning them to the supplier, reworking them, or scrapping them.
- Documentation: Maintain detailed records of all non-conforming materials, including the nature of the defect, the root cause, and the corrective actions taken.
5. Continuous Improvement:
- Data Analysis: Regularly analyze data on incoming material quality to identify trends and areas for improvement.
- Corrective Action: Implement corrective actions to address any identified problems and prevent recurrence.
- Preventive Action: Implement preventive actions to proactively prevent quality problems from occurring.
- Feedback to Suppliers: Provide regular feedback to suppliers on their performance, including any areas where improvement is needed.
By implementing these measures, I can ensure that the incoming goods meet the required quality standards, minimizing the risk of defects, reducing production costs, and improving customer satisfaction.